Checklist
How is Cement Manufactured?
Cement manufacturing is a sophisticated process that incorporates thousands of variables. It is vital to maintain integrity in the manufacturing process to ensure cement quality is maintained. It is important for you to how cement is manufactured to get a good grasp of the sophisticated steps that go into it. Different categories of cement are manufactured with varying ratios of raw materials. These variations bring forward a diverse set of properties for each category of cement.- Extracting Raw Materials: The first step involves removing the raw materials from the earth using heavy machinery. Generally, raw materials like limestone and clay are extracted from quarries by blasting and ripping.
- Crushing and Transportation: Wheel loaders and dumper trucks carry the extracted raw materials to crushing zones where the rocks are crushed to necessary segments for further processing.
- Preparation of Raw Materials: The crushed raw materials are transported to storage facilities, where it remains until further processing. Conveyor belts, cableways, etc., are used in this case. The desired raw mix of crushed materials and additional components required for different categories of cement is prepared using metering devices. Roller grinding mills and ball mills grind the whole mixture to a fine powder.
- Burning: The raw materials are burned at approximately 1450 degrees Celsius in preheated kilns. This process, also known as sintering, creates a new clinker material.
- Clinker Grinding: The clinker is cooled down and stored in clinker silos after burning. Ball mills or roller presses ground this clinker into an excellent powder-like substance. Some additives like gypsum and anhydrite are used depending on the cement category.
- Shipping: The finished product is then transferred to other storage facilities. Different strengths and categories of cement are grouped in separate silos. From there, cement is packaged and distributed all over.
- Quality Assurance: The whole manufacturing process is strictly monitored by hi-tech computers and sensors. Experts analyze cement samples in different phases to identify impurity or bad quality products. Good quality control measures are essential in any cement manufacturing plant.
What is the Importance of Choosing the Right Cement in Bangladesh?
Choosing the right cement in Bangladesh is of utmost importance as it can guarantee the endurance of a construction project. Good quality cement will resist environmental degradation and save costs on future maintenance. The quality of cement determines the lifespan and integrity of your building. So, choosing the appropriate cement for your specific construction requirement is a very crucial step in ensuring the quality of your dream house.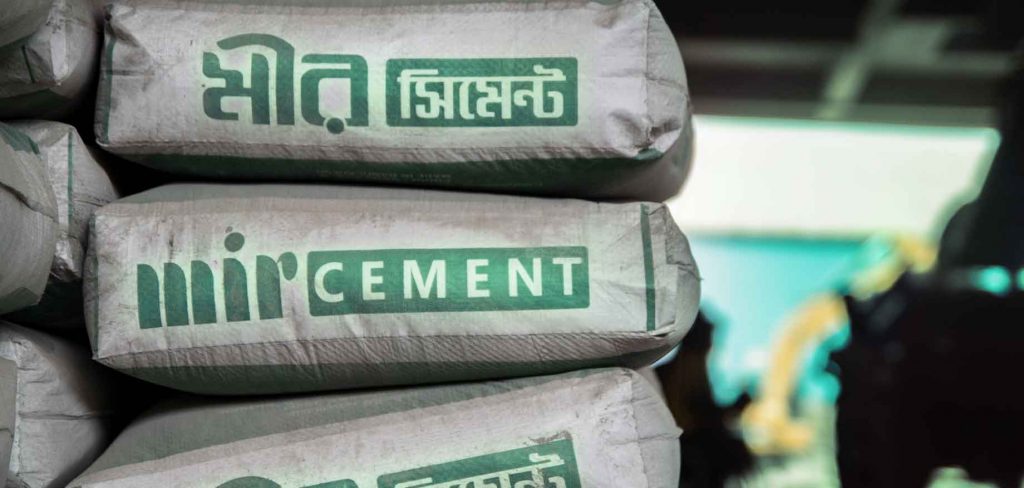
- OPC offers higher resistance to shrinkage and is less prone to cracking in the future.
- It offers a faster setting time. Hence, it is more productive.
- Curing duration is very short in OPC, and it can save a lot of money.
- OPC has less durability than PPC/PCC, as it is less fine and has higher permeability.
- OPC is more difficult to pump due to its less cohesive strength.
- OPC is costlier than PCC/PPC.
Which Cement Types to Use in Building Construction?
The area of application determines what type of cement to use. A list of the common application area and cement categories will help you to make your decision:
Application Area |
Cement Type |
All RCC Structures | OPC Grade 43 OPC Grade 53 |
Masonry, Plastering, and Tiling | PCC/PPC |
Decorative Portions | White Cement |
Foundation for Poor Soil Quality | Sulfate Resistant Cement |